Surfaces For Punching Tools
Surfaces For Punching
Before I get into surfaces, there are few other factors that can affect punching. First off is good support. There needs to be solid support underneath the punching area to minimize bounce and absorption of the force of the punch penetrating the leather. Some people punch over the leg of work bench rather than the middle. Other supporting surfaces can be something like a stump or section of tree trunk. You can also use something with some mass to help prevent bounce. Large anvils or metal plates work well as a surface support. I use a granite inspection plate on one bench that does have some flex and the mass of the granite helps to negate the flex and bounce.
The second factor is the weight of the striking tool. It is the length of the cutting edge of the punch that determines how much force will be needed to punch through. Obviously a 1 inch round punch will require more force than a 1/8 inch round punch. Complexity of the punch factors in after that. A 1-1/2 inch round punch has about 4.7 inches of length. Each scallop on a 1-1/2” rosette or concho punch adds more length and the total length of edge increases by about 40% more than the comparable round punch. Obviously the more length of a punch edge, then a heavier striking tool or more force will be required to punch.
Finally - Surfaces. I want my punches to cut cleanly and completely through the leather and lightly penetrate the punching surface. That gives me a complete cut all the way around and no sections of uncut leather that pull and feather. The three major materials I recommend are plastic, shoe sole material, and heavy scrap leather. For plastic I prefer low-density polyethylene (LDPE). This material is available at most plastic and commercial kitchen suppliers. A large share of the cutting boards sold at department stores are LDPE also. The low-density polyethylene boards will allow penetration of the punch edge without being hard enough to damage the edge. The shoe sole material I prefer is the black type sold in sheets. Some leather suppliers sell it small sections and call it “poundo board”. You can order it from many shoe repair suppliers as well. Personally, I buy it in 18x36 sheets that are 5/16 inch thick. It is relatively inexpensive as well. The final surface I like is a piece of heavy scrap leather. This allows a nice clean punch for smaller punches and it is easy to pull the punch from the material.
My particular choice of material depends on what I am cutting. The poly boards are a bit slick and tend to slide around more. That said, they are my choice for most small round punches, strap end punches, and small to medium bag punches. The sole material is grippy and stays in place. I like it for all my larger punches and especially rosette punches. Smaller punches tend to stick in sole material more than larger punches so that is a consideration. For finer punches like very small round punches and especially lacing chisels, I prefer scrap leather. The scrap leather is a very forgiving surface and in my experience punches pull out easier.
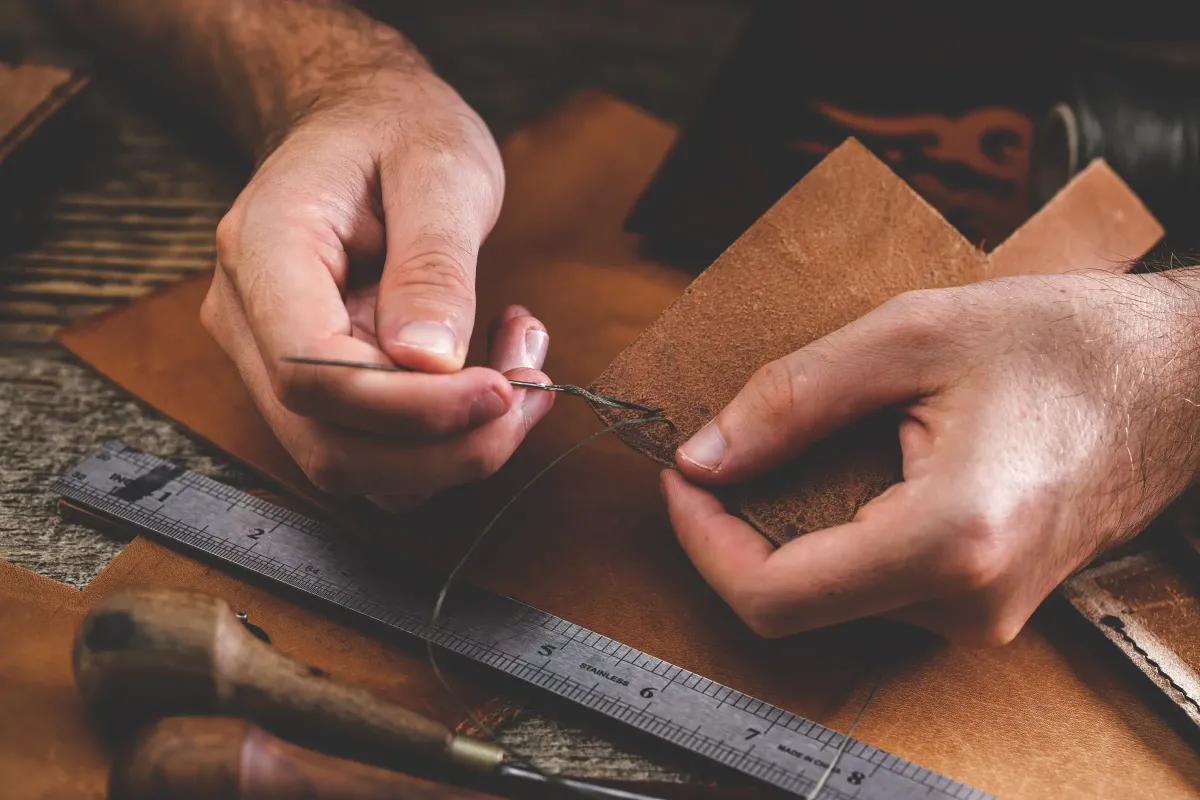
- January 8, 2025
Selecting Vintage Edge Creaser Sizes
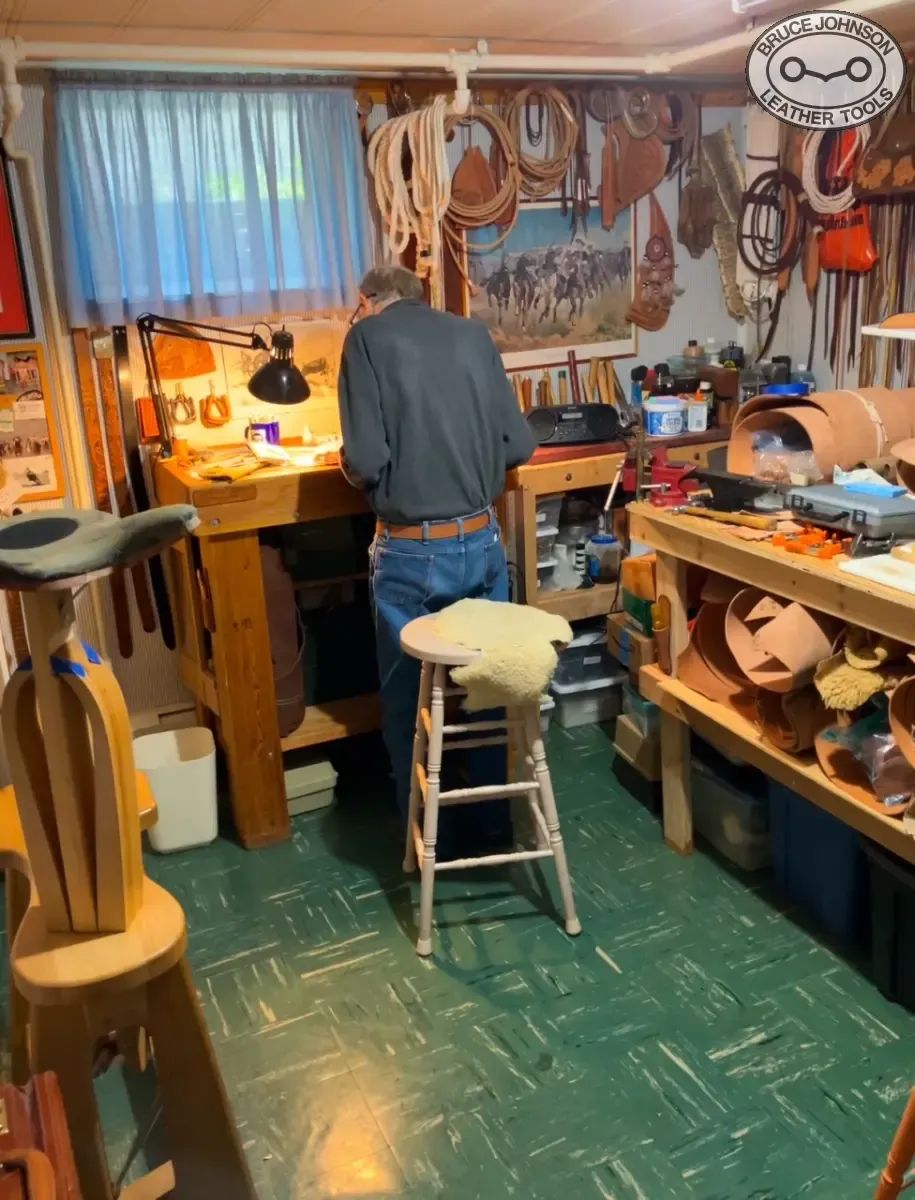
- January 12, 2025
The Last Day
- January 18, 2025